Planning Making the Press
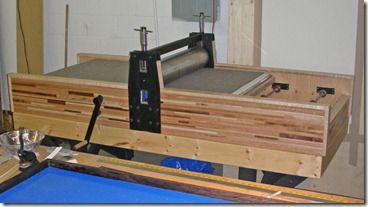
The concept of using only metal where the pressure needed, can help it easier and cheaper to
make presses. My small press is convertible to either etching or lithography – even having linear offset system for litho. My press is much more complicated to build and uses a drive motor.
After working on his litho press with me, Jacob decided that he would like a large etching press for etchings as well as relief prints. We talked it over to decide the size and other features he wanted included. Since I had made a smaller convertible for my daughter who as teaching art at the time, it was a proven concept that just needed to upsized. The principal of making just the pressure area from steel was accepted as Jacob had woodworking facilities at home to finish off the construction.
The Rollers
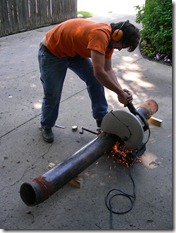
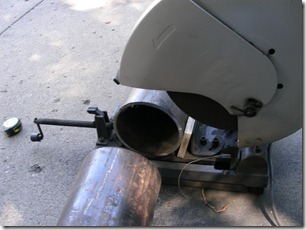
Cutting and trimming a large diameter steel tube is best done with an abrasive cutoff saw. My saw would not cut all the way through, so the tube was rotated to cut sections at a time.
The first thing to consider was the two rollers, the possible diameter and method of construction. As there are two scrap metal yards in the city, we went to them to see what kind of steel tubing was available. We found suitable 3/8th inch thick steel tubing that was 6 inches in diameter; for two lengths to make a 30 inch wide bed. The first thing to do was to cut the tubes to size - using a cutoff disc. The tube where then trimmed to length, leaving a little for final truing on a lathe.
It was decided that we would use a high quality shaft as the Brandt press at the university had broken when a student had put too much pressure on the rollers. When I went to my friend who owned a machine shop, he came to look at the damage and told me the steel was likely a number XXXX which should have been YYYY, that he had in his shop. I told him that the outside tube might be supported with a doughnut-like ring inside, which would make it impossible for him to replace the shaft. We took off the roller and in week or so, called me that it was fixed with the better steel shaft and a trued new surface on a lathe.
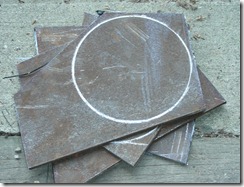
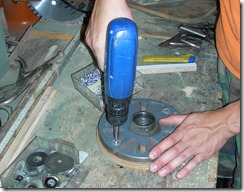
The steel had to be cut in straight lines, then trimmed to fit unto the wooden support screwed to a faceplate. The center of the intended disc was first placed touching the point of the tailstock, then four screws were set into place. A hole was drilled and expanded with a boring tool to fit the diameter of the shaft.
We decided to reinforce the tube from the inside with doughnut rings, so the 1/4 inch sheet steel from the scrap yard was sectioned to make six rings - one on the inside of each and two for the ends. The cutoff saw was used to separate the pieces and trim them closer to a circle. The best way we thought of making the donuts was to cut out a plywood disc and screw it unto the faceplate of the lathe. Four holes to screw the sheets unto the plywood on the faceplate was all that was needed to produce center hole that was made to fit the shaft, using a boring tool.
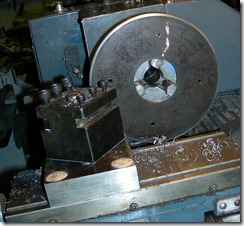
The plates were transferred to a three jaw chuck to lathe the outer edge that would fit inside the roller tube. You will notice that I have made a more solid tool holder as I had found the original tool post was not really ridged enough, which I only use when needed for angle cuts. The block will take both 1/4 and 1/2 inch bits, considering the project.
Roller Assembly
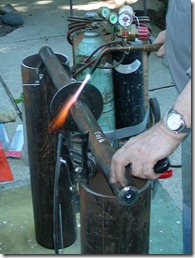
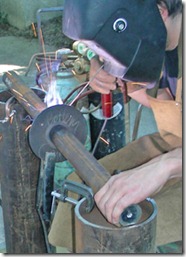
The discs fit the inside with little room to spare because of the welded seam produced in the manufacturing of steel pipe. The shaft was one of the most expensive part of the press because of special features needed to prevent it breaking.
Since it was summer and nice outside, we decided to move welding outdoors since I could easily get power to the 110 VAC arc welder from a power plug near the basement window. Since the chosen steel could become brittle from arc welding and extreme local heating, we used an acetylene torch to preheat the shaft before arcing the ring into place.
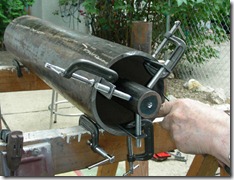
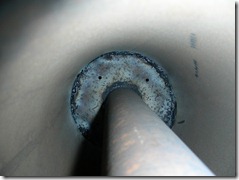
After drilling centers on the shaft, we were prepared to weld the pieces together. Jacob did most of the welding, using my underpowered 110 VAC unit that was allowed in residential areas.
With the center support and one end welded to the shaft, it was inserted into the tube and centered with three improvised threaded rods clamped to the tube edge. The other end was shimmed to place the shaft perfectly in the center and then welded into place. The clamping support was removed and the center ring was welded to the tube by holding the welding rods vertically. Now the other end ring could be used to close up the end by again using small shims to get it as perfect as possible.
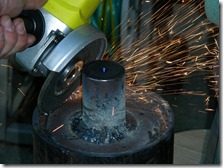
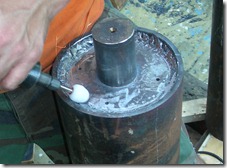
Using disc grinders and round grinding points, the rough but still strong welds were smoothed out.
Since my small 110 volt welder was inadequate for thick metal, the welds are not cosmetic but strong enough for the stress. Some grinding and filling with body putty made a decent looking set of rollers. One of the shafts is longer at one end to accommodate the gear to turn the bottom drive roller.
Since my lathe was too short for this set of rollers, we took them to an industrial metal shop that trued the surfaces and shaft ends cut to size. As they didn’t seem to have a belt sander on hand, they used a disc sander that produced the unsightly surface.
Bearings
One could use ball or roller bearings, but to keep costs down, we used the bushing system similar to what I used on my convertible press. It was more work but a learning experience for us as well. We decided to use two inch long bushing that set the dimensions of many other parts, like the upright supports and wooden sides of the press.
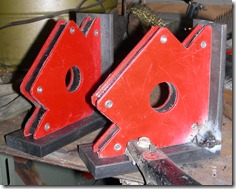
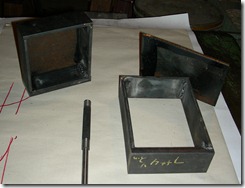
Welding the boxes needed to support the bronze bearing, which are more than good enough for slow turning and the pressure needed for printing an etching. The heavy support of the bearing was need for Jacobs press as I did not use that feature with my smaller rollers.
The first thing was to make metal boxes with support for the Oilite bronze bushing. The sides were made from 2" wide steel 1/4" thick, while the end taking pressure was 1/2 inch. The piece were welded together using magnetic holders to get perfect square units. Sheets were cut to fit inside the boxes and welded into place from the inside. A thicker piece of steel was cut to length and one end ground with an inside curve that fits the bushing diameter.
My lathe does not have an indexing feature, so to hold the chuck solid, I used two clamps.
The hand grinder has a attachment for use on a lathe, making it possible for us to grind a curve.
There would be hardwood filling the space with the grain running horizontal to accommodate any side pressure put on the bushing; this was done by gluing two pieces of oak at 90′ to each other to get the required thickness for the box. The piece of steel that was ground to the curve of the bushing was welded into place - after the hole to accept the shaft for the drive gear was made by drilling and filing smooth. The other three bushings did not need this effort.
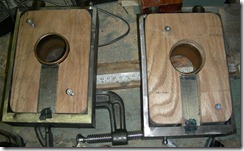
Much fitting and adaption of materials was necessary to get the bearing strong enough for a press.
The wood pieces were fitted as close as possible by using temporary screws to put out the sections as we worked. Epoxy was used to glue the wood and metal box together - but it was necessary to keep the epoxy from flowing into the interior of the bushing by using a paper tube lathed to size and pushing it tightly against the metal backing. Grease nipples were added after drilling through the wood and the bushing, for future lubricating of the press.
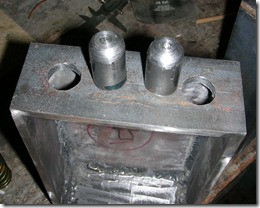
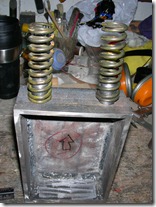
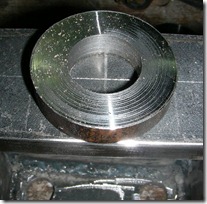
Construction of the bushing holder seems complicated, but it would be nearly as complicated to use commercial ball bearing as done on manufactured presses. All dimensions would be different.
Holes had been drilled at the ends that held short rods unto which strong spring were used to keep the rollers apart. You will notice the different lengths of the boxes that give us space to keep the drive roller off the bottom of the completed press. The top roller bushing needed a ring to hold the threaded rod that is apply pressure. This was welded on and the sides ground off to the thickness of the box.
Frame Supports
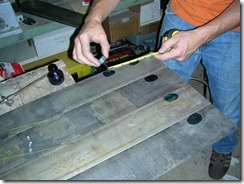
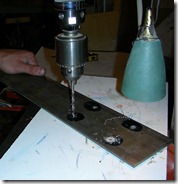
Marking, drilling and cutting the angle for the taper at the top of the bearing supports.
The framework to hold the bushings and pressure system were constructed from the 2" wide flat steel and also 3" wide material for the outside. The top was tapered by cutting off a piece 1 1/4" and 8 " long at one side. Holes were drilled for the bottom bushings and two more to connect to the wooden sides of the press. Holes at the tapered end were added to accept metal cross pieces holding the pressure screw and top cross bar
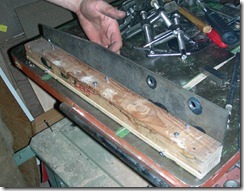
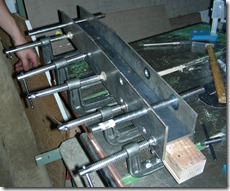
It is important to use jibs for assembling a number of similar pieces. It need not be complicated but well thought out by using common materials in the workshop.
A jig was setup to make sure the supports were identical and accurately welded together. The basis for the jib was just a piece of scrap lumber planed to the width of two inches - the same the the bearing thickness. A series of screws keep the metal off the wood as the welding heat would burn the lumber. Rods were inserted into the holes where bolts go and the pieces adjusted to get perfect 90′ angle in all directions. Then they were welded together by first tacking the metal to prevent warping in the long weld.
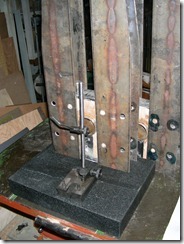
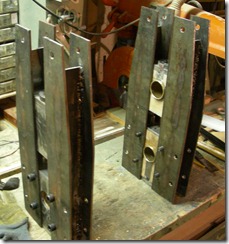
Before drilling the holes into the bearings, we used a gauge on a machinist granite block to make sure the distance from the bottom was the same on both sides.
Holes were drilled in the bottom bushing and the supports temporarily bolted together to make and weld the upper assembly. It consisted of short joining flat metal and spacers to fit the 2" spacing set for the bushing boxes. Nuts were welded on one side of the supports to accept bolts that would tie the two side supports together.
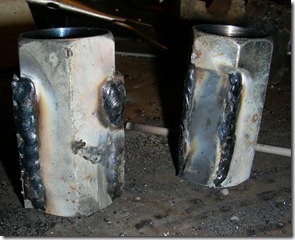
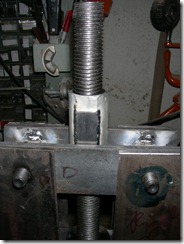
The coupling devises were fitted between the support, then lathed to accept the vernier column before welded in place. There may have been easier ways of doing this, but this worked out.
A threaded coupling "nut" was made wider by welding on pieces to opposite sides, then ground flat to fit nicely in between. One end was lathed circular to accept a piece of aluminium tubing that was engraved with spacing lines (more later) for setting pressure accurately. This was done by putting in a short section of threaded rod into the lathe chuck and screwing the coupling unto it - making it perfectly centered. All parts welded together - as well as the spacers.
Vernier Pressure System
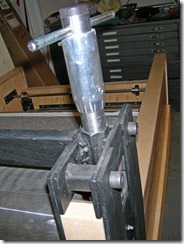
This was a luxury feature that is included in the better presses to make pressure setting accurately. It consisted of aluminium tubing that fit inside one another. The smaller pieces were lathed on the inside at one end to fit the top of the threaded coupling used to apply pressure. It was then engraved on the lathe by using a pointed tool for longitudinal “0†line and the shorter spacing lines.
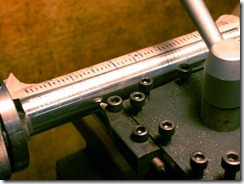
I used a small 3-jaw chuck from my Unimat to hold the tube between centers, using a larger bullnose at the tail stock. It was easy to make the long vertical line by working the tool along the lathe bed. The short lines were transferred from tape spacing by turning the chuck by hand, using the square handle that comes with chucks.
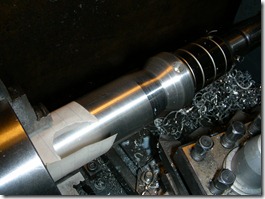
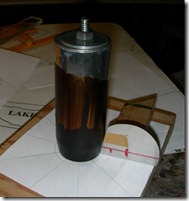
Using the lathe to make the division on the vernier was our way of producing the working system.
The finer increments allowed by the division of 360′ was done on the larger tube. One end was given a slight angle by setting the tool post to produce the short taper. A sheet of paper was produced with lines 36′ apart with a circle to make sure the tube is centered. A special small piece of metal, with an angle equal to the taper on the tube, was secured to a handle to make sure the line would be vertical. Then the soft ground was scratched with a needle and etched in copper sulfate mordant. Numbers were stamped above the lines with a standard set of punches.
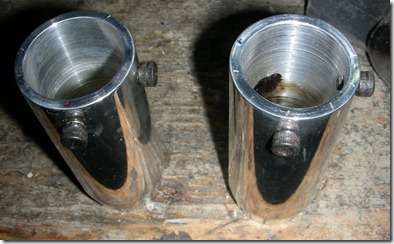
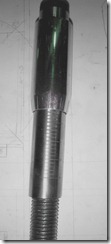
The components making up the vernier pressure system that was epoxied into place on the press.
Two screws were put at the top to adjust the vernier for setting the zero point. The threaded rod was capped by lathing another coupling to fit the inside of the larger tube just finished. It was cut in half and screwed to one end of the heavy threaded rod. A hole was drilled through it and the rod for a short piece of thinner rod forced and glued into place to help adjustment. The two screws would grab unto this small section as it went down when turned; the graduation would be 1/10th the pitch of the treaded rod. Jacob topped it off with a piece of ebony lathed to fit.
Frame Assembly
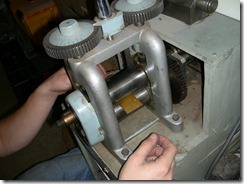
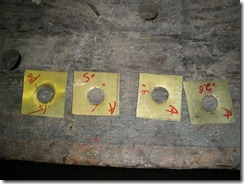
The assembly of the supporting frame and drive roller required some spacers, so Jacob used my rolling mill to produce shims that fit the exact thickness for each bolt. Holes were punched and the brass hammered flat to slide in. The cross piece connecting the two frames at the top was now cut to length from a piece of rectangular tubing and welded unto respective sections; ready to assemble the press. This was the distance set by the length of the rollers and bearings.
Adjustable Bed Support
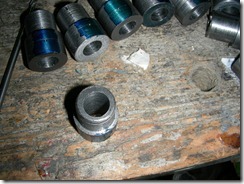
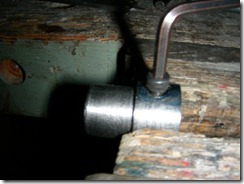
Making many fittings for the support of the press bed. Epoxy was easier than precision lathing.
What is usually used on presses is an offset method that adjusts a bearing or wheel to just hold up the bed evenly as it goes through the rollers. Short pieces of rod were cut and lathed at one end to fit the inside of ball bearings that we picked to act as wheels. They were then put into the lathe chuck with a piece of metal against one of the jaws to produce an off center hole to allow the adjustment needed. Two holes were drilled and taped to set the height of the wheels. The bearings were epoxied to the end and later put unto long rods that had flat pieces of iron welded at each end. These were dropped into holdup slots attached to the inside of the press walls. The total length was exactly the distance between the two wooden sides and screwed at a height that would allow for adjustment.
The Wooden Press Sides
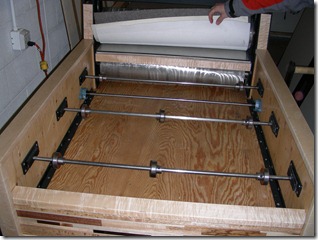
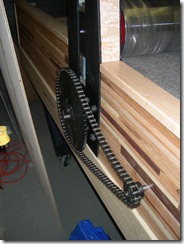
The press in place at Jacobs’ first studio - and has been moved many times since being built.
At this point Jacob took the rollers and frame home to work on the rest of the press. He used plywood unto which he assembled assorted hardwoods to produce an interesting surface. The press bed was made of hardwood unto which a 1/4†piece of aluminium was used for a perfectly flat surface. You can see the bed support wheels within the body of the press. Pillow blocks were added to transmit the handle energy to the opposite side of the press, where a simple reducing system of a chain drive was used. The bottom has become a storage space for blankets and such, holding quite a bit of material where it could be easily accessible.
I am sure Jacob and his father took some pictures on their work of building the wooden frame and assembling the final press, but I have never seen them. Since the woodworking is simpler in such a project, I feel there has been enough information given for some printers to take on building a press.
If there are any questions about some part of the project, please get back to me directly on my e-mail as the registration system has been dismantled because of spams etc. I will be posting an article on my small convertible press, which is much more complicated, having to employ an off/on pressure system required for scraper bar lithography.